
9 CULTURE CHANGES
Driving Digital Transformation for Manufacturers
While an Industry 4.0 transition will involve using new technology tools to streamline your processes, increase quality, reduce costs and enhance profitability, a change in company culture will be the sure way of transiting successfully to Industry 4.0.
We are at the dawn of a new era of industrial revolution characterized by connected devices, the application of computers, artificial intelligence, robotics, and other smart technologies.
This new era is commonly referred to as Industry 4.0. It is about digital transformation in the manufacturing and production industries that enhance value creation processes through modern technology.
The term Industry 4.0 acts as the synonym for the fourth industrial revolution. It represents a new stage in the control of the industrial value chain. Industry 4.0 is no longer the future, but it is the present.
We are witnessing enormous and smart innovations that increase efficiency, streamline production, and shift the way manufacturing is done.
Experts working in different industries agree that this revolution is fundamentally different from what has been witnessed before because technology is advancing quickly. Also, the challenges that come with these changes are complex and diverse.
According to experts, Industry 4.0 has had a significant impact on income levels and the global economy and will improve the quality of life due to new products and services to millions worldwide. For instance, today, we are witnessing the benefits of the digital world via telemedicine, digital wallets, online shopping, and much more.
Some of the technologies fueling Industry 4.0 include additive manufacturing, cyber security technology, big data and analytics, the industrial internet of things, autonomous robotics, and simulation.
To take advantage of Industry 4.0, organizations often embark on digital transformation that includes investing in new technologies, upgrading technical infrastructure and modifying daily procedures and operational processes. While these are important steps in a company’s digital transformation journey, a truly successful digital transformation starts by putting people at the center. Workplaces must prioritize a culture that embraces change and life-long learning.
Transformations are typically hard, and so are digital transformations. Digital transformation could fail for different reasons.
- Lack of support from the management – Digital transformation is a big change and requires the support of the top leaders.
- Lack of a leader/champion – Someone to oversee the project is required
- Departmental infighting – The changes will affect everyone and will require collaboration.
- Lack of resources – Resources are required to implement digital transformation.
- Attempting to do too much too soon – Digital transformation is a process and requires using a scaling model.
- Lack of flexibility/ features – Digital transformation should be flexible to address the current and future needs.
- Lack of communication/support/collaboration – Your partner should be trusted to guide you in the digitization process.
- Lack of existing processes – Digital transformations need to deliver some level of consistency.
The following are some of the changes in culture that can drive digital transformation in the small and medium-sized manufacturing industry.
- A Culture of Conflict Resolution
A recent survey established that 30% of companies that have successfully shifted to digital transformation train their employees on technical knowledge, new mindsets, and behaviors.
If you wish to succeed in digital transformation, you must change your organizational culture and find where conflicts of mindset and digital culture clash. If your company culture and digital transformations are not aligned, expect a loss of productivity and slow adoption of the new changes.
- Adaptability
Small and medium-sized manufacturing companies need to cultivate a culture of adaptability to promote a transition to Industry 4.0. Employees may take time to adapt to the new changes, especially if they find nothing wrong with the organization's current status.
A common misconception is that when your company adopts technology, it has achieved digital transformation. In reality, digital transformation is not just about software or technology but about how your entire team adapts to the new changes. Thus, organizational culture is vital for the success of your digital initiative.
Remember that your employees are the key drivers of digital transformation. The executives and especially the C-suite leaders should clearly define the company's vision and strategies to realize digital transformation. They should establish concrete goals and point the organization in the right direction. Additionally, they must ensure that each employee understands and embraces the digital initiative.
Melissa Henley, a senior director of customer experience at Keyshot, a global software company in product design, states that true digital transformation occurs when the entire organization aligns with its digital strategy.
She says the digital transformation initiative should not be for the executive but the whole workforce. According to her, if decisions about digital transformation involve all employees, it's inevitable that the initiative will succeed. Cultural change is an essential element in digital transformation that will make technology relevant, and it will help shift the new changes.
- Collaborative Culture
Digital transformation in the small and medium manufacturers cut across all departments because structural and institutional changes affect each employee.
For successful digital transformation, the role of each department in the initiative should be clear. In addition, there should be a solid professional collaborative culture and strong leadership for this initiative to succeed.
The company executive team should assume the coordination and communication role and prevent any disruption or misunderstandings arising from different departments.
- Top Management Should Champion the Initiative
Although top management may lack the technical background in most cases, they should know they need not be cheerleaders but lead from the front to make digital transformation a reality.
For instance, employees want to see the CEO and other leaders in the C-suite using tools like data analytics. Mainly digital transformation fails if the top leadership fails to champion the course. In addition, the leadership should allocate sufficient resources to make the initiative a reality.
- Demonstrate Listening
Companies that effectively manage digital transformations should engage their employees to feel like part of the team. They have to ensure that the voice of every employee matters.
One of the best ways is to listen to recommendations and suggestions from the junior employees and train them on better ways of communication.
In addition, they should empower employees at all levels of the organization, which doesn't mean you will have double opinions in your organization. Still, you'll have cross-functional teams offering input to the executive team about company policies and business operations.
- A Culture of Innovation
Most companies don't lack people with innovative ideas, but most of these individuals are scared to put forward their ideas because they are working in companies that don't tolerate failure. Many innovations in the past were a result of many instances of trial.
Small and medium manufacturing companies need to cultivate a culture of innovation and embrace failure to find new and workable ways of coming up with solutions to their client's problems.
Even today, the best products in the market start with failure, but as innovators re-think, they refine the concept to come up with superior solutions.
Company leaders should promote innovation by celebrating small successes by innovators and tolerating the setbacks. Also, they should place them in programs that encourage employees to voice their ideas fearlessly.
- Measurement
Successful digital transformations are not possible unless a company has systems and ways of measuring its effectiveness. Some of the ways that the company can measure the initiative's effectiveness are through skills like innovation, creativity, agility and adaptability, and productivity. Top management should encourage and reward creative problem solving and innovation.
- Training
Gen Z workers prefer working in technology companies, but they will not overlook manufacturing companies that rely on robotics, automation, and other technological advances. Small and medium manufacturing companies can tap on this workforce by showcasing their digital transformation and plans for the future.
In addition, they need to motivate their young workforce to upgrade their skills to match the new technologies. This culture will ensure they have skilled workers available today and in the future.
Companies that are moving in this direction can achieve technological transformations much faster. The manufacturing companies need to meet the expectations of today's workers and attract a broader range of candidates.
- Enhanced Communication
It's a common misconception that automation will kill many jobs, and this is not true because automation will lead to many new opportunities.
At the introduction of computers, most people thought secretaries would lose their jobs, but this wasn't the case. The secretaries adapted and upskilled to adjust to the new technology and boost their careers.
The same will happen to the manufacturing sector, people will not lose their jobs, but they will find new ways of doing their jobs better through Industry 4.0.
Your Journey to Industry 4.0
As you transition to industry 4.0 in your manufacturing company, it's helpful to think of where your organization is today and plan for the future. A successful transition will involve using the new tools to streamline your processes, increase quality, reduce costs and enhance profitability.
A change in company culture is a sure way of transiting successfully to Industry 4.0. Company executives need to realize this fact and use it to move into the future.
|
|
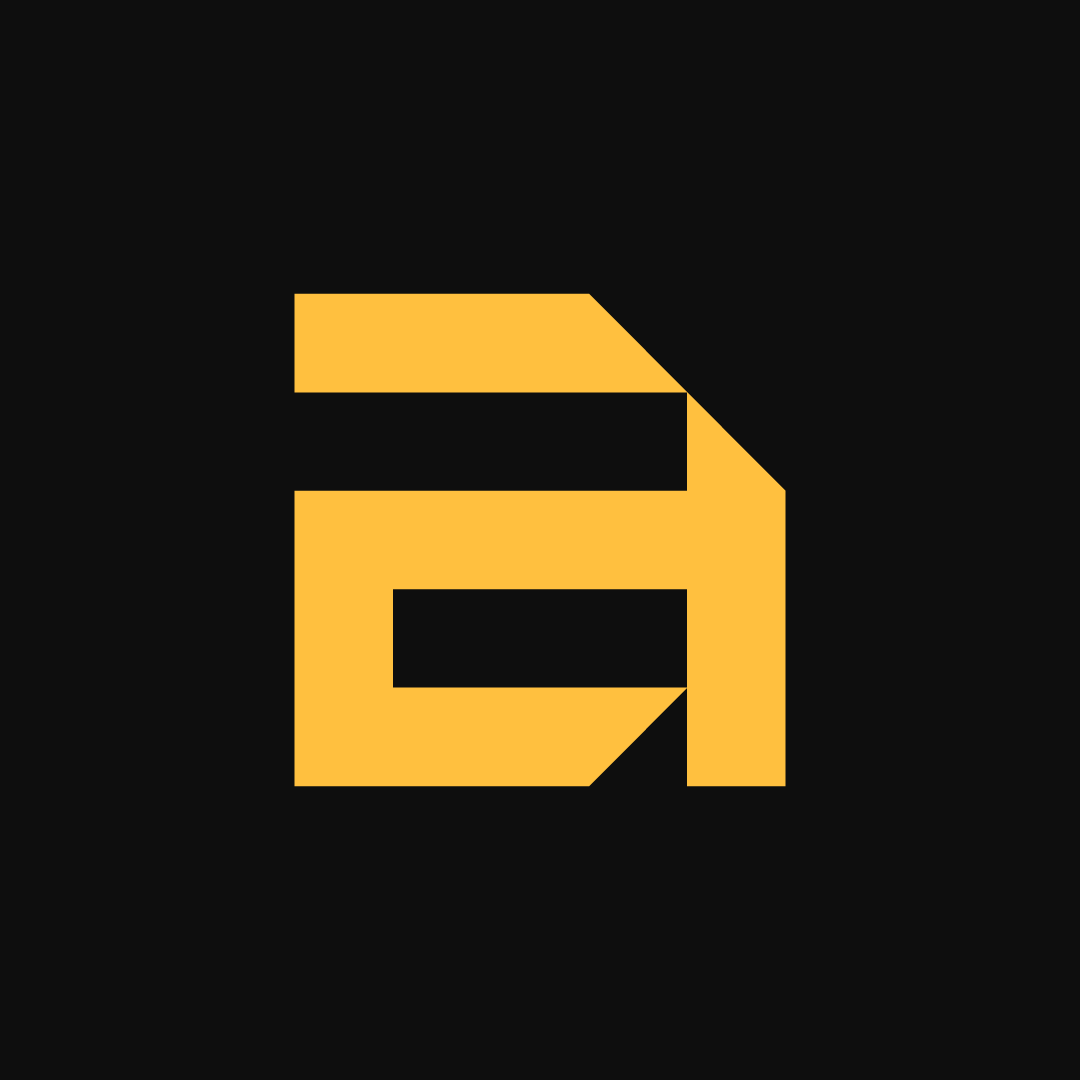
Automation Alley is a World Economic Forum Advanced Manufacturing Hub (AMHUB) for North America and a nonprofit Industry 4.0 knowledge center with a global outlook and a regional focus. We facilitate public-private partnerships by connecting industry, education and government to fuel Michigan's economy.
Photo by ThisisEngineering RAEng on Unsplash